This article will give you an insight to understand the distillation column operation. Also, you will understand the effect of subcooled reflux temperature on distillation column process. The reflux temperature is very important as this affects distillation column energy requirement and throughput as well.
As we all know, distillation columns are widely used to separate the liquid mixture based on their boiling point difference. Higher the difference in boiling point, easier the separation and vice versa. A distillation column has trays or packing inside, which provides the multiple equilibrium stages for heat & mass transfer. Moreover, inside column liquid & vapor phases remain at saturated condition. In other words, liquid remains at its bubble point and vapor is at its dew point. Therefore, in a distillation column we have highest temperature at the bottom and lowest at top side. To operate a distillation column, you need generally three types of utilities as below:
- Hot utility (Such as steam, thermic fluid etc.), to supply heat through reboiler
- Cold utility (Like cooling water, chilled water etc.), to remove heat through condenser and chiller
- and, Electricity for driving feed, bottom, reflux pumps, etc.
So, we can see the operating cost of a distillation column is sum of all above three variable costs. Moreover, one distillation column can separate 2 components only in its pure form. In case of if there are N components in a mixture, we need N+1 column in series to separate them.
Table of Contents
Instrumentation & Controls in Distillation Column
Below figure can help you to understand a typical continuous distillation column control system in our industries. Here we can see one feed stream and two output streams, namely distillate stream from top and bottom product from bottom of the column. However, in some installations you can see multiple input streams and more than two output streams as well.
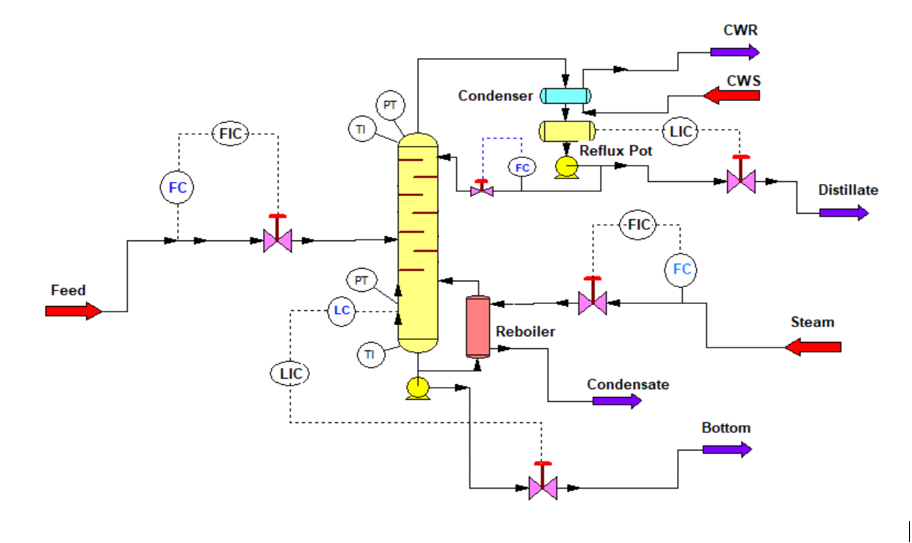
Critical Parameters in a Distillation Column
As we have discussed earlier, the objective of a distillation column is to separate a liquid component mixture. At least one component comes in desired pure form one end and other end contains remaining components. The objective is to maintain the purity of one stream and no or minimum loss of pure component in the second outgoing stream. Therefore, to achieve our objective there are following parameters which are critical and their precise control is important.
- Feed flow rates of the column and it’s temperature
- Steam flow rate to the column reboiler
- Reflux flow rate and it’s temperature
- Reflux pot level
- Column bottom level
- In case where column is operating under pressure or vacuum, control of column pressure.
- Column top and bottom temperatures
Available levers to Control the Critical Parameters
- Feed control valve – to control feed to the column
- Reboiler steam feed control valve – to control column bottom temperature, which indirectly control the concentration in the bottom product
- Reflux flow control valve – to control the column top temperature, which indirectly controls the purity of top product
- Column bottom control valve – to control the sufficient column level, which is critical for normal and efficient operation of reboiler. It affects the column boil up, bottom product composition and column pressure
- Reflux pot level control valve – this controls reflux pot level, which is important for constant flow of reflux to the column. In case of any disturbance in level will disturb the reflux flow rate, subsequently column temperature, column pressure and top product purity will be disturbed.
- Column pressure control valve – very important to control the column temperature profile and disturbance will change the column throughput. Further this will disturb the top and bottom product purities.
- Cooling water flow and temperature control – cooling water supply temperature depends on wet bulb air temperature and we adjust flow rate manually. However, this manual adjustment is not frequent.
Present Control Philosophy and Challenges
- In present scenario all the control valves operate in single loop control manner. In other words, control valve takes care to control that particular variable only. However, we can integrate control loops using cascading of ratio control method for advance control strategies.
- All the control valves are operating to maintain their respective set point variable independently. These set points are feed flow, steam flow, bottom level, reflux pot level, reflux flow and column pressure.
- This set point is static and the plant SOP gives this value. If anything goes beyond the control rage of the set point. Operator take the control from auto mode to manual mode.
- To bring the column operation in normal mode again operator’s role is very important. Generally, this manual operation depends on the intelligence of operator and his experience.
- Disturbance in one control loop disturbs all other control loops, which take too much time to restabilize the whole operation back to the normal levels.
- All controls loop are feedback control loops, where disturbances are detected after entering into the system and then controllers take charge to restore the present values back to the setpoint values.
Now let us understand the impact of reflux temperature on column energy requirement & capacity with help of an example.
Operating Conditions of Example
For our case we will consider as feed mixture containing two components benzene and toluene. This column is used to separate 5000 kg/h of a mixture containing 60 wt% benzene and 40 wt% toluene. Top product purity is 99.995 wt% benzene and 99.99 wt% toluene in bottom product. Feed temperature is 50 0C and reflux ratio for the column is 1: 3. Column is operating at atmospheric pressure.
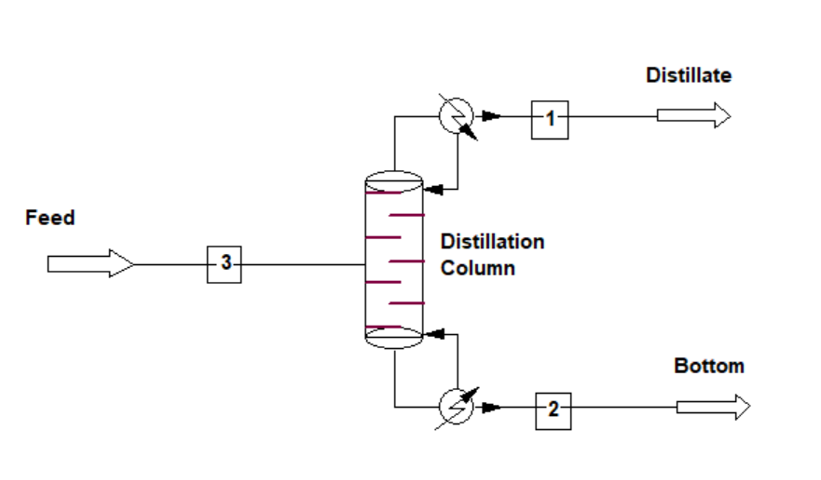
Distillation column material balance and other properties of all streams are as below:

Heat Duty Calculation for Column at Saturated Reflux
Let us calculate total heat input at column reboiler for above operating conditions. This is also known as reboiler duty and can be estimated as below:
QR = Feed preheating heat load (AQ1) + Heat requirement for column boil up (BQ2)
AQ1 = Mass flow rate of feed * Heat Capacity (column bottom temperature – feed temperature)
AQ1 = 5000 * 0.41 * (113 – 50) = 129,150 kcal/h
BQ2 = Distillate mass flow rate * (Reflux Ratio + 1) * Latent Heat of Vaporization for Distillate
BQ2 = 3000 * (3 + 1) * 94 = 1,128,000 kcal/h
Therefore, reboiler heat requirement will be,
QR = AQ1 + BQ2 = 129,150 + 1,128,000 = 1,257,150 kcal/h
Above steam calculation is for the saturated reflux temperature. In actual we don’t have temperature control at condenser. Therefore, process fluid outlet temperature is far below than saturated liquid temperature. In other words, we can say column reflux remains at subcooled condition. And, this subcooling can be around 6 – 8 0C plus to the condenser cooling water outlet temperature. So, for our case condenser cooling water temperature is 36 0C hence reflux subcooled temperature will be around 42 – 44 0C.
So, let us consider subcooled reflux temperature, Tr = 44 0C. Therefore, we are feeding reflux at subcooled conditions and subcooling is of (80 – 44 = 36 0C). Fundamentally, it is important to note that an input stream’s temperature and composition to the distillation column must match to input point column inside conditions. This is very important for the distillation column efficiency and energy effectiveness. The impact of reflux subcooling can be understood as below:
Heat Duty Calculation for Column at Subcooled Reflux
Now again imagine above column operating at subcooled reflux instead of saturated reflux. Since the subcooled reflux temperature is at 44 0C and inside column saturated temperature is 80 0C. Which is the top vapour temperature and distillate saturation temperature as well. So, when this subcooled reflux will enter into the column. Reflux mass will take heat from the vapour inside by condensing it to get saturated. This way there will be additional refluxing inside the distillation column. This is also called internal reflux and is cause of additional heat load and lower column throughput or capacity.
Therefore, additional heat load required for reflux preheating inside the column can be estimated as below:
Q3 = Reflux mass flow rate * heat capacity * (distillate saturation temperature – reflux subcooled temperature)
Q3 = 3000 * 3 * 0.44 * (80 – 44) = 142,560 kcal/h
Hence, Q3 is the additional heat load on column reboiler, which is Q3*100/(QR + Q3) = 10.2% of the heat load when reflux is at saturated condition. In other words, if we increase reflux temperature, column steam requirement can be reduced by 10% from the present subcooled reflux condition.
Moreover, subcooled reflux affects column throughput also. In our example for saturation condition column throughput will be as below:
Throughput, V = distillate flow rate * (reflux ratio + 1) = 3000 * (3 + 1) = 12000 kg/h
Because of subcooled reflux situation column vapour condensation inside column is V’ = Q3/(distillate latent heat of vaporization) = 142,560/94 = 1517 kg/h
Which is 1517*100/12000 = 12.6% of column throughput at saturation conditions. Therefore, we can say at subcooled reflux column capacity reduces by 12%.
Conclusion
Finally, you saw the quantitative impact of subcooled reflux on distillation performance. Also, we find out the available energy reduction opportunity is around 10%. And, around 12% capacity release is possible from subcooled reflux level.
You can use this analysis to identify the improvement opportunities in your plant. For this you can collect the data of reflux temperature and plot the line chart to visualize the variation. This way you can find out the possible improvement scope. To elevate reflux temperature you can work out following options:
- Throttling of cooling water supply to minimize the sub cooling of reflux.
- Condenser tube plugging option can be worked out. As in most of the cases we have excess area available in condenser.
- Other option can be provision of two smaller condensers in series for required condenser area. In this first condenser process outlet goes for column refluxing and outlet from second condenser is distillate.
- Provision of reflux preheating using column vapor through installing a heat recovery exchanger.
Also we can look into the possibilities of heat integration of distillation columns to reduce overall energy consumption. Moreover, above discussion is valid for batch distillation column also.
Thanks for reading, please write to me in case of any clarification required.