To manage effluent generation and its treatment in Chemical manufacturing has been a major challenge for every chemical manufacturer. This challenge is becoming tougher and tougher day by day, as these effluents impact the environmental ecosystem adversely. And we all know environmental sustainability is the need of hour for every manufacturing industry. Therefore, this is our moral responsibility to maintain an ecological balance in our planet’s natural environment. So that we can conserve natural resources to support the wellbeing of current and future generations.
So, to achieve above objective every chemical process industry must be energy efficient to minimize their carbon foot prints. Moreover, need to reduce the effluent generation during chemical manufacturing. This we can achieve by adopting zero discharge policy, be it for any type of effluent. However, as a chemical manufacturer selection of a technology is very important, where effluent generation is minimum. Also, selection of effluent treatment methodology is equally important to make the manufacturing facility zero effluent discharge. In this article we will discuss various types of common effluents generation during chemical manufacturing and their possible treatment methods.
Table of Contents
Various Types of Effluents Generation
We can broadly categorize the effluent or waste generated in chemical manufacturing in four types as below:
- Liquid Waste – This can be of different type based on chemical compositions present in water. Like Aqueous effluent containing acid impurities like HCl, H2SO4, HNO3, etc. Other can be Aqueous effluent containing organic impurities such as benzene, ethanol, acetic acid, pyridine, etc. Apart from this Aqueous waste having impurities of various salts like NaCl, Na2SO4, MgCl2, NH4Cl, etc. Other types can be the various combination or mixture of above effluents. The sources of these wastes, can be the processes like extraction, decantation, centrifuge or ANF washing mother liquor, neutralization, etc.
- Organic Waste – This is also in liquid form but in some cases at lower temperature can be solidified also. An organic residue is mix of high boiling organic compounds or contain tarry material. In chemical industries organic residue mainly generates from the bottom of a distillation column.
- Solid Waste – It can be semi-solid also like slurry or wet cake containing moisture or other chemical in the range of 5% to 30%. The examples of solid waste are activate carbon, reactor catalyst, inorganic salts (i.e., NaCl, MgCl2, Na2SO4, etc.). The final discharge points for these wastes are solid-liquid filters, sedimentation tanks, centrifuge, ANF, ATFD, etc.
- Gaseous Effluent – The source of this effluent stream in chemical plant we can see from absorber column top, spray dryers, vents of heat exchangers, vessels and tanks. Many times, this effluent is not harmful for the environment and we can discharge it into the atmosphere without any treatment. But in some cases where it contains chemicals such as ammonia, organic solvent, reactor off gases mixture of various toxic organics, it requires treatment before venting into the atmosphere.
Effluent Treatment Methodologies
We select effluent treatment methodology based on the type and characteristics of the effluent. Below are some common techniques to treat the effluents in our industries:
Liquid Waste Incinerator
This incinerator we use to treat the aqueous waste containing organic impurities, which are not biodegradable and we can not treat this using ETP. As we can not discharge or recycle the waste water due presence of hazardous chemicals in it. Therefore, for treatment of such effluents we use incinerator.
In Liquid waste incinerator there is a combustion chamber which operates around at 800 to 850 0C temperature. In case of the presence of chloride impurities in waste water we need a secondary combustion chamber also. This secondary combustion chamber operates at around 1100 to 1150 0C temperature to incinerate chloride chemicals. The fuel inside the incinerator can be furnace oil or natural gas. Hot flue gases subsequently pass through a waste heat boiler and we can generate waste steam, which we can used inside the plant. After waste heat boiler flue gas passes through economizer where combustion air required for incinerator is preheated and flue gas passes through chemical scrubber to remove the NOx and SOx impurities before discharging into the atmosphere at safe location.
We use liquid waste incinerator for the incineration of Liquid Organic Waste and Vent Gas also. As organic waste and vent gas has good calorific values, therefore it reduces overall fuel consumption for the incinerator. Below is the schematic sketch of a Liquid Waste Incinerator.
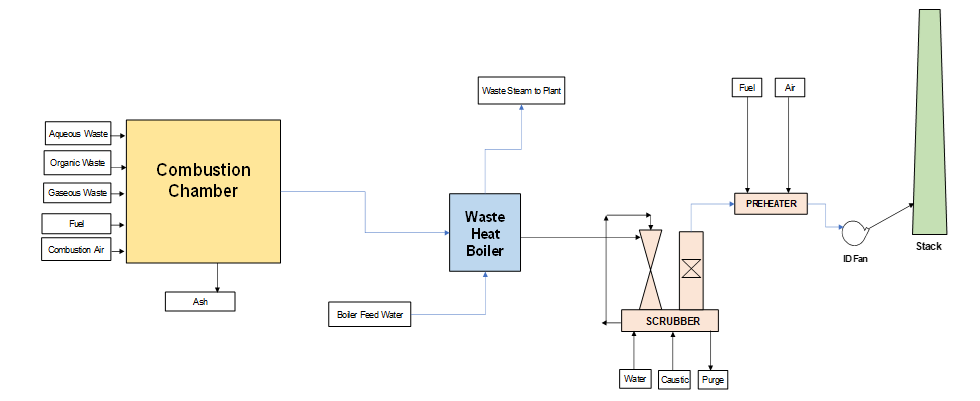
Solid Waste Incinerator
It is similar as above shown only difference we require one pyrolizer or Rotary kiln before incinerator combustion chamber. In rotary kiln we charge solid waste through a conveyor, this kiln rotates at very low RPM between 0.5 to 1 rotation per minute. The temperature of kiln or pyrolizer is maintained around 800 to 850 0C by burning fuel through fuel burners. All the organic material present in solid waste burn and remaining non-combustible solid discharge from other end of the kiln. Hot flue gases enter into next combustion chamber where temperature is further increased around 1100 to 1150 0C to incinerate chloride impurities. Subsequently follow the similar path as described in Liquid Waste incinerator.
The solid waste which non-incinerable is send for secured land fill sites, however this not a suitable method of waste disposable. Below is the photo of a solid waste incinerator installation.
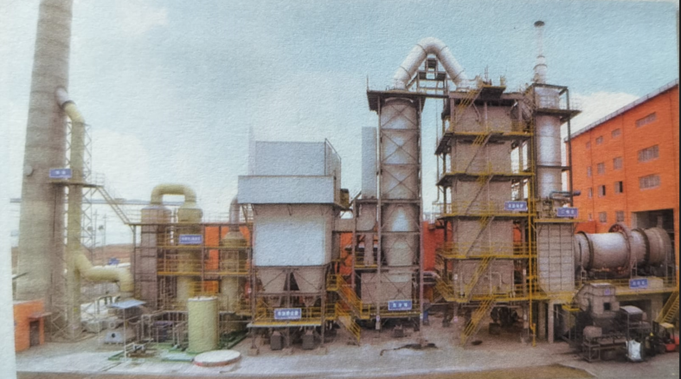
Dioxins are not usually present in waste, but they can form when chlorine-containing organic substances are burned. Modern incinerators produce dioxins and furans from three points in the process: stack-gas emissions, bottom ash, and fly ash. Operating Incinerator at higher temperatures above 1100°C is considered the most effective way to destroy dioxins.
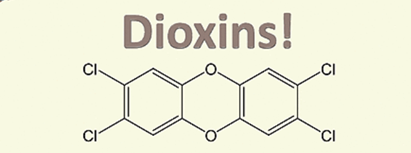
Presence of Dioxins in our environment can cause cancer, reproductive and developmental problems, damage to the immune system, and can interfere with hormones.
Spray Dryer for Inorganic Aqueous Waste
In case when inorganic salts are presents in aqueous waste such as NaCl, MgCl2, Na2SO4, we can use spray dryer chamber. In this case we do not produce waste steam and here we use a spray chamber in place of the waste heat boiler. Rest other equipment remain as it is as liquid waste incinerator. Here hot flue gases at 800 to 850 0C coming out from the combustion chamber enters into the spray dryer. Aqueous inorganic waste is sprayed through a nozzle from top, water gets evaporated and comes out with flue gases while dry solid salt is collected from the bottom of spray dryer. Which can be reused or sold depending on the quality otherwise goes for secured land fill sites.
ETP for Waste Water Treatment
We use Effluent treatment plants (ETP) for the removal of high amounts of biodegradable organic compounds, tar, debris, dirt, toxic, non-toxic materials and polymers etc. from the industrial waste water. The typical process steps for a ETP are as below:
- First remove any oil or tar from liquid surface through grease trap,
- Addition of flocculant to enrich organic matter in wastewater,
- Filtration and collection of solids (solid waste)
- Destroy large organic molecules in wastewater using oxidation methods,
- Adjust PH 7-8 with sodium hydroxide and flow into anaerobic process,
- Effluent passes through aerobic tank, converting all organic molecules into carbon dioxide, water and biomass (sludge) which we can be remove from the effluent.
Subsequently mass flows into a sedimentation tank and air flotation machine to remove biomass/sludge.
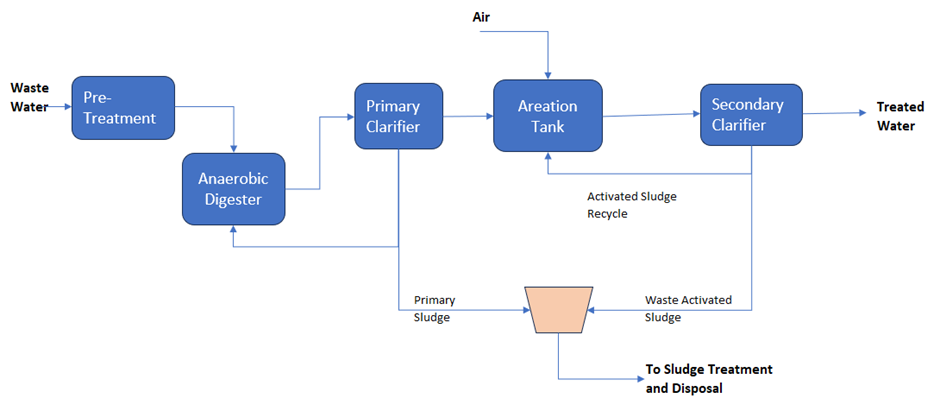
The waste water which contains non-biodegradable chemicals such as insecticides, pesticides, synthetic fibers, pyridines, cyanopyridines, ammonical impurities, glass objects, mercury, lead, arsenic etc., we use incineration method for treatment.
Conclusion
Effluent treatment technology is a continuously evolving field and require new ecofriendly and energy efficient ways. Because treatment of effluent is a cost and it reduces profit margin. Simultaneously, engineers should keep on working to reduce the effluent generation inside the plant using new technologies. Also, we need to look into the recycling of the effluent so that final effluent quantity is minimum for treatment requirement.
Thanks for reading…