In almost every chemical plant we use distillation column to separate the components based on their boiling point difference. Also, we know distillation columns are the major consumers of steam & cooling water utilities. Therefore, to increase the contribution margin of the product it is necessary to minimize energy requirement in distillation process. We can minimize energy consumption for distillation columns operating in series by their heat integration. We will discuss this scheme considering an example of solvent recovery plant.
Table of Contents
Problem Statement
For our study we will take example of separating the mixture of acetone, benzene & toluene. In SRP (solvent recovery plants) there are two columns in series Col-1 & Col-2. The feed rate to Col-1 is 3000 kg/h and contains acetone (30%), benzene (30%) and toluene (40%) on weight basis. Col-1 feed inlet temperature is 45 0C. For heat transfer between streams consider minimum temperature difference 15 0C.
For heat integration between columns Col-1 will be operating at 0.6 bar and Col-2 will be operating at 1.7 bar. At these conditions Col-2 top temperature will be 97 degC and Col-1 bottom temperature will be 77 degC, which suffice our minimum temperature difference requirement between both the streams. The vapour from Col-2 will be used in Col-1 reboiler as a heating media.
We will calculate utility requirements for both the cases. In first case we will estimate utility consumption without heat integration of the columns. In second case will discuss columns heat integration scheme and will calculate the utility requirement.
Case:1 (Columns Without Heat Integration)
Process flow diagram for the system is as below, where pure acetone is coming out from column top. The bottom of Col-1 is being fed into Col-2, here pure benzene is coming from top and 99% pure toluene is coming from bottom.
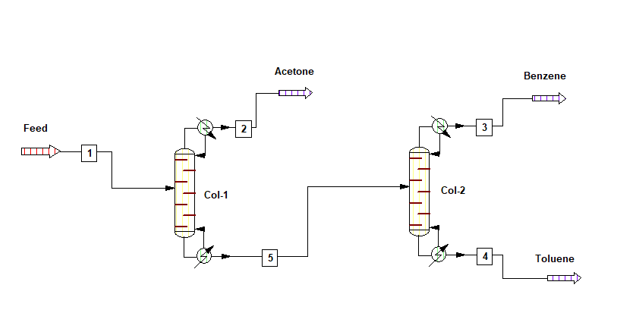
Material Balance without Heat Integration
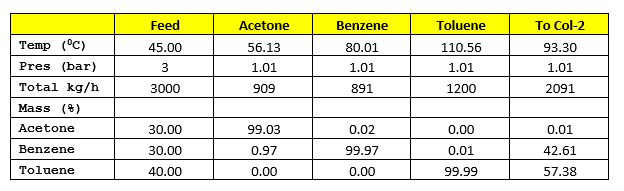
Col-1 is operating at a Reflux Ratio of 1 : 8, hence vapour rate from the column will be V1 = (1 + 8) * 909 = 8,181 kg/h. Latent heat of vaporization for Col-1 distillate is 122 kcal/kg and heat capacity of column feed is 0.46 kcal/kg-0C. Hence, heat load on condenser will be
Q1cond = V1 * 122 = 8,181 * 122 = 998,082 kcal/h
Heat load on reboiler can be estimated as below
Q1reb = Q1cond + 3000*0.46*(93.3 – 45) = 1,073,016 kcal/h
Col-2 is operating at a reflux ratio of 1 : 2, therefore vapour rate from the column will be V2 = (1 +2) * 891 = 2673 kg/h. Top product latent heat of vaporization is 94 kcal/kg and heat capacity of Col-1 bottom product is 0.46 kcal/kg-0C. The Col-2 condenser heat load will be
Q2cond = V2 * 94 = 2673 * 94 = 251,262 kcal/h
Heat load on reboiler can be estimated as below
Q2reb = Q2cond + 2091*0.46*(110.56 – 93.30) = 267,864 kcal/h
Summary heat load for columns
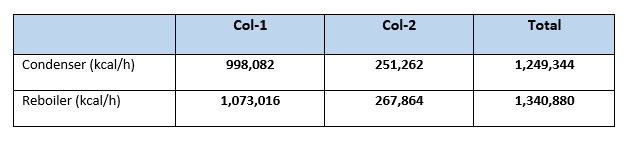
Case:2 (Columns with Heat Integration)
By heat integration of Col-1 & Col-2 we can minimize the overall energy requirement for the solvent recovery plant. Process flow diagram for the system is as below, in this Col-1 is operating at 0.6 bar & Col-2 is at 1.7 bar. Col-2 vapour at 98 0C will be used as a heat utility in Col-1 reboiler.
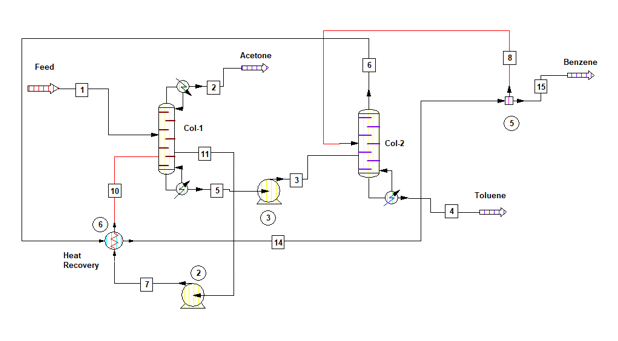
Material Balance for heat integrated columns
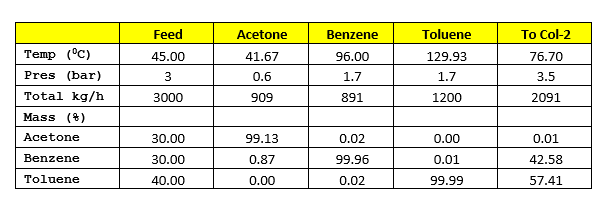
Latent heat of vaporization for Col-1 top product is 125 kcal/kg and heat capacity of column feed is 0.46 kcal/kg-0C. Hence, heat load on condenser will be
Q1’cond = V1 * 125 = 8,181 * 125 = 1,022,625 kcal/h
Col-1 reboiler heat load can be estimated as below, in this column we are adding heat from Col-2 vapour. Since Col-2 reflux ratio is 1 : 2, hence vapour flow rate will be V2 = (1 +2) * 891 = 2673 kg/h. Col-2 top product latent heat of vaporization is 91 kcal/kg
Q1’reb = Q1’cond + 3000*0.46*(76.70 – 45) – V2*91
Q1’reb = Q1’cond + 3000*0.46*(76.70 – 45) – 2673*91 = 823,128 kcal/h
Col-2 is operating at a reflux ratio of 1 : 2, therefore vapour rate from the column will be V2 = (1 +2) * 891 = 2673 kg/h. Top product latent heat of vaporization is 91 kcal/kg and heat capacity of Col-1 bottom product is 0.46 kcal/kg-0C. The Col-2 condenser heat load will be
Q2’cond = 0.0 kcal/h (as total vapour of Col-2 is condensing in Col-1 reboiler)
Heat load on Col-2 reboiler can be estimated as below
Q2’reb = V2*91 + 2091*0.46*(129.93 – 76.70)
Q2’reb = 2673*91 + 2091*0.46*(129.93 – 76.70) = 294,443 kcal/h
Summary heat load for columns in this case
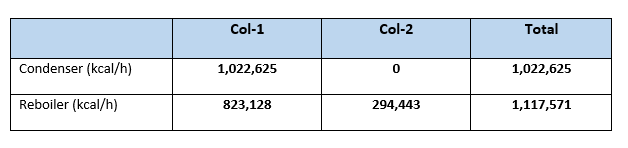
Conclusion
From our calculation it is clear that net condenser duty for Case:1 is 1,249,344 kcal/h in comparison with Case:2 it is 1,022,625 kcal/h. So, reduction in condenser duty is (1,249,344 – 1,022,625 = 226,719 kcal/h). This is 18.14% reduction in condenser duty or in other words we can say reduction in cooling water requirement to the condensers.
Similarly, the reboiler heat load reduced from 1,340,880 kcal/h (in Case:1), to 1,117,571 kcal/h (for Case:2). Which is reduction of 223,309 kcal/h in overall reboiler duty, this is 16.65% reduction from Case:1. Or we can say 16.65% reduction in steam reduction which is a big annual savings. For our case study steam saving will be (223,309/490) = 455.7 kg/h. Considering cost of steam 1.30 Rs/kg annual savings will be (455.7*1.30*24*330) = 4,691,887 Rs.
In above calculations we have considered reflux temperature is at saturated condition. However, in actual operation it mostly subcooled. Therefore, it add surplus heat load to the reboiler duty and condenser duty also. Energy conservation is very important for the sustainability of any industry and we all must keep continue to work in this direction.
Hi,
Thanks for the blog. Nice article and explained nicely.
I have a question related to calculations. In case 1, you have calculated vapour flow rate using R value as: V=(R+1)*D. However, you have mentioned that reflux ratio is 1:8 which means: L=1 & D=8 right? This leads to R=1/8=0.125. Therefore, V=(0.125+1)*909=1022.6 kg/h. Please correct me if I am wrong. I would like to understand, why you have considered V=(1+8)*909? Unless R=8.
Hi!!!
Please note in a column R is the ratio to Liquid going inside the column to the distillate which we draw as a product. So, it is R= L/D = 8, now what will be the V= vapour mass flow rate coming out from the column, it is V = L + D, right.
So we can rewrite this V = R*D + D = (R + 1)*D. In my calculation 1:8 means L=8 and D=1, you are interpreting it other way. This is the only difference in understanding. Inn industry we use this terminology to mention the reflux like 1:2, 1:10, 1:0.5 etc. where first number represents distillate ratio while second term is reflux ratio. I hope I could answer you? Thanks!!!