In current competitive market scenario, there is a huge pressure on the product margins and production capacities. This situation is posing big challenges for business heads to retain their current market shares as well as getting new customers. Therefore, continuous process improvement is a major challenge for the manufacturing team, which is a requirement from business heads. And, is necessary to reduce the variable cost of production and enhance the plant productivity. Moreover, it is top most priority to run the plant with complete safety and meeting all environmental compliance.
Table of Contents
Improvement Areas in Chemical Plants
In plants manufacturing team consistently keep on looking for the improvement opportunities to meet the business strategic goals. The various available improvement areas inside a plant can be as below:
Plant productivity enhancement
For the products where demand is high, we need to see how can we get maximum production from the existing assets. Also, we need to look into the areas to reduce waste and focus on the recovery section optimization. Many times, when few equipment is bottleneck stage in plant, we replace them to get higher capacities from the same installation. In such cases generally we get simple payback of less than 6 months. Also, working on the yield of reaction is a good idea, this will give two-fold benefits reduces variable cost and increase the capacity as well.
Raw material (RM) norms reduction
This area of work is very important from the strategic point of view for a company. Whichever company take proactive actions to work on the RM norms reduction are always ahead in the market competition. Generally, raw materials cost contributes around 80% of the total product cost. So, reduction in norms will improve the bottom line of the company remarkably. To reduce RM norms, we can look into the increasing product recovery. Reactor process parameter optimization and variation reduction techniques gives excellent results. Also, we must look into the process intensification, this will reduce the parameter variation and enhance the product quality with consistency. For example, wherever we are using batch reactors must look into the possibilities to replace it with plug flow reactors or loop reactor.
Utility norm reduction
Second big area to reduce variable cost of production of a product is utility section. Plants consumes many types of utilities such as, steam, power, Cooling water, Chilled water, Brine water, Hot oil, etc. Among these steam and power are two major contributors to the utility bill. Further, we can divide the improvement opportunities in these area in two parts. First is called generation side and second is known as consumption side.
- For the steam generation side is boiler house and this includes distribution network also. We should see opportunities for boiler efficiency improvement and distribution loss reduction. On consumption side which is plant area we can look into the opportunities of heat integration, pinch analysis and waste heat recovery techniques such use of VAHP. Apart from this we can look into the possibilities to use heat pumps is distillation and converting LP Steam into high pressure steam. Also, where ever we find a high pressure fluid stream available, can be used to run liquid jet pumps or ejectors.
- In case of power we can look opportunities in loss reduction in transformers and distribution losses. At for consumption side we can look into the improving pump efficiencies by anti-friction lining on inside casing and impeller of cooling water circulation pumps. Opportunity of replacing motors with high efficiency motors. Analysis of cooling water distribution network will give us insight to reduce the overall power consumption of the plant by minimizing the head loss.
Effluent handling and treatment cost reduction
For any plant effluent treatment is an environmental compliance and must to do responsibility. Moreover, it is utmost important for the company’s sustainability. Because, chemical plants are source of all type of effluents (i.e., liquid, solid and gas) which are very harmful for the living beings and environment also. So, plant team is responsible for effective effluent handling and effluent treatment with minimum cost. To achieve this objective following can be the possible ways:
- We can see the options to reduce effluent generation at source. For this we can apply pinch technology to see the possibilities for recycling effluent streams within the plants. This will reduce the fresh water consumption and overall effluent generation quantity.
- For treatment of effluents, we must look into cost-effective technologies. As, effluent treatment is very energy intensive process so it is imperative to develop an energy efficient process. Various effluent treatment process used by chemical industries are such as, incinerators, thermal oxidizers, RO plants, MEE with ATFD, catalytic oxidation process, etc.
Other improvement areas
Apart from above there are other areas in plants where we can take up the process improvement by implementing Lean methodology. Various areas include as below:
- Supply chain process – we can look into the lead time reduction at both end i.e., at supplier and customer side. This will reduce the inventory in process and will increase the cash flow. Trucks demurrage cost reduction is a good project. Raw material and finished good freight cost optimization are good opportunities. Packaging material and packaging cost reduction also contributes in product cost reduction.
- Spare parts & consumables inventory – in plant maintenance this is an excellent opportunity for cost reduction. Here, we can take a Lean project to minimize the inventory which is cost to the company.
- Finished goods & raw material warehouse inventory – Here inventory reduction project will bring huge benefit to the organization by optimizing inventory levels. This will increase the cash flow for company.
- Manpower productivity – can be assessed by conducting time & motion study. This will help the management to deploy their resources effectively and efficiently. In result productivity per person will increase and overall cost to the company will reduce.
Process Improvement Methodologies
Now we will discuss here two widely used process improvement practices in chemical plants. First is Lean and second is Six Sigma or DMAIC methodology. If we look into details then we can divide the improvement opportunities in two type of categories. They can be either waste reduction or variation minimization in nature. In case where we want to minimize the waste, Lean principals are applicable. For the case of variation reduction DMAIC or Six Sigma approach is helpful. Both these techniques are widely used methodologies in chemical industries.
Lean manufacturing is also known by lean production or Toyota Production System (TPS). The Toyota Production System was first implemented in Toyota around in 1930. Taiichi Ohno is the founder of Toyota Production System (TPS). Six Sigma was originated by Motorola in 1987, which was focused on product quality improvement.
What is Lean Methodology?
Lean is the process improvement methodology for continuous waste reduction inside a process. Using Lean we can produce products and services, faster and at a lower cost. In Lean practice we can divide various wastes inside any process in seven types of categories abbreviated as DOTWIMP.
- Defects
- Overproduction
- Transportation
- Waiting
- Inventory
- Motion
- Processing
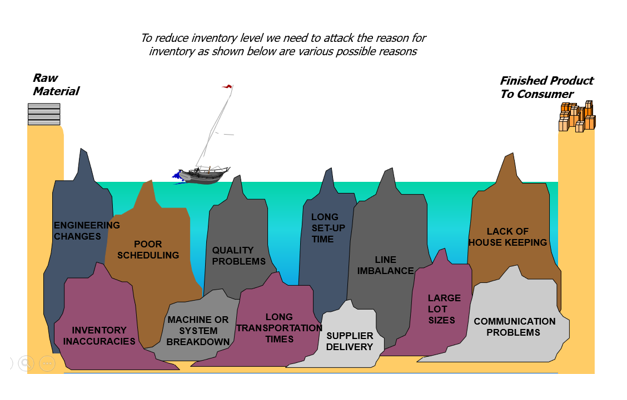
Steps to Implement the Lean Methodology
Project Selection
First step is selection of the project, we should take up those projects which are of strategic importance for the company. Also, the areas and products where Lean implementation will make bring huge financial benefits.
As is Process Mapping
In this step we prepare the process flow of existing process. Here, we break the process steps in small-small activities. We collect the data for each and every activity and estimate the cycle time for present value stream map. This cycle time is the base line for our improvement process. Next, we segregate these activities in value added or non-value-added categories. To know about the activity type ask one question, “whether customer is paying us for that or not?”, if answer is yes then it is a value added otherwise considered as non-value-added activity. However, we have many non-value- added activities also which we need to perform from statutory point of view. These activities includes such as plant safety, environment and health, company social responsibility etc.
Analyze Step
After as is process map is ready now, we identify the wastes in process map using seven types of waste (i.e., DOTWIMP). This identification helps us to eliminate these wastes from the process and we get an improved process map. This revised process map is also known as future state value stream map. The cycle time of future state value stream map can be as low as 1/3 of the present state value stream map in many cases.
Implementation Step
We implement the solutions to eliminate all type of wastes as identified in earlier step. Change in standard operating procedure is done and necessary training are provided to the operators. So that improved process implementation is smooth and performance is sustained. Change management is very important for the success of any project. Because we can make changes in machines easily but adoption of changed process by operators is very difficult. Therefore, applying change management techniques are very important, this will answer the plant team, “What is in it for me?”.
What is Six Sigma Methodology?
Six Sigma is a statistical tool to reduce variations in any process. In Six Sigma we convert a real-life problem into statistical problem and then find the statistical solution using statistical tools. This statistical solution is converted into the real-life solution. In other words, six sigma is a process improvement tool which is based on statistical analysis and followed by engineering solutions.
As we discussed Lean was developed to minimize the waste in a process, Six Sigma methodology was developed to minimize the process variation and improve the product or service quality. According to Six Sigma the quality definition is, “Hitting the target and minimizing the variation”.
Lean implementation is very important for a successful Six Sigma project implementation. Because, Lean makes sure we are working on the right activities, and then Six Sigma makes sure we are doing the right things, right the first time.
Six Sigma
- The term ‘Sigma’ taken from Greek alphabet, it Is used to designate the data distribution or spread about the mean.
- Sigma Capability Is a metric which indicates how the process is behaving. This process can be business or manufacturing. Higher the Sigma value, better the Process Capability which is a defect free work.
- Sigma is the measure of process variability.
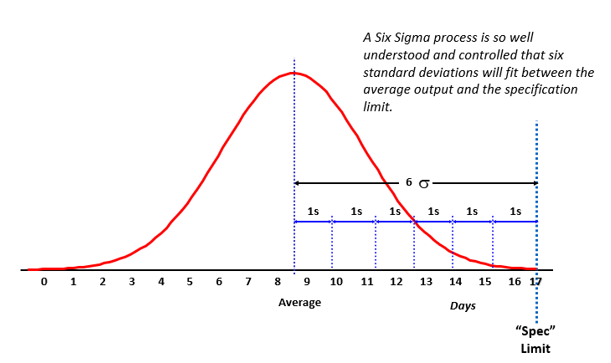
When we talk about Six Sigma it means our process yield is 99.99966% or in other words, we can say our process has 3.4 defects per million of opportunities.
Steps in Six Sigma Methodology
Six Sigma is a systematic approach, uses statistical tools for process variation reduction. Various steps in this methodology can be defined as DMAIC which is described as below:
Define Phase
This is most important step to start a Six Sigma project. We must take up that project which is very important to meet the company’s strategic goal. Project must be discussed with all the stake holders as this is a team work not an individual project. We must remember that Lean or Six Sigma projects require a cross functional team, because we need people having different skill sets such as operation, statistics, project management, design, instrumentation, R&D etc.
Here we identify the project ‘Y’ and collect the data to set the project baselining. The final document for Define phase is called Project Charter. A project charter should include below information:
- Business case – Why this project is important for the business?
- Problem statement – How big is the problem?
- Goal statement – What is the project including baseline and target?
- Project sponsor, mentor, six sigma black belt person, team member, project leader names.
- Project time lines showing start and completion dates for all the DMAIC phases
- Estimated investment and potential benefits from the project
Measure Phase
In Measure phase we identify the X’s for our project ‘Y’. In other words, we find out independent variable for our dependent variable using various tools such as Fish Bone Diagram, Brainstorming, Tree diagram, etc.
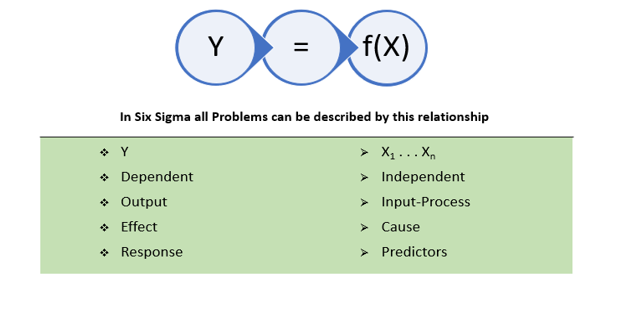
After identifying all the cause variables, we take up the data collection plan. Before this MSA is very important to eliminate the error because of measure system. Any measurement system includes instruments and data capturing so it is necessary to estimate the accuracy level of both. After MSA (Measurement System Analysis) we collect the data from our process for our independent variables.
Analyze Phase
In Analyze phase we do validation and verify our all the identified X’s using statistical techniques. This cause validation step tells us about the effect of X’s on our Y, we get few important significant variables which are important for the variation in Y variable. After getting our critical variables we conduct the DOE (Design of Experiments) for our project. DOE is the experiment conducted in controlled environment to validate and optimize the independent variables. At the end of Analyze phase we are with our optimized parameters (X’s) which will give the best output (Y).
Improve Phase
The Improve phase is all about implementation of the identified solution after discussion with the domain experts. In this we discuss with the team our solution implementation plan and do the risk assessment. After implementation and commissioning we move into the Control phase of the Six Sigma methodology.
Control Phase
We make the changes in standard operating procedure of the process and provide necessary training to the relevant team members. For this, we use control charts to see the process variation and compare it before improvement stage. After demonstrating the performance, we close the project and submit complete project report to operation excellence or business excellence head.
Conclusion
Lean & Six Sigma are excellent methodology for process improvement in our plant processes and we all must learn it. Both these techniques use the power of data analysis. I have described both the techniques in brief here. However, I will try to explain them in my future posts. In case you need more information please feel free write to me.