As a Chemical Process Engineer, we are suppose to do equipment costing to evaluate the equipment fabrication quotations received from various equipment fabricators. These equipment are like shell and tube heat exchangers, distillation columns, agitated vessels, jacketed vessels, decanters, storage tanks, etc. This equipment costing exercise gives us clarity about the equipment cost, which we can use as a basis for further negotiation with the fabricators before placing the purchase order. So, in this article I will be discussing the costing method of a shell and tube heat exchanger. Also, I will share one excel sheet link which you can use for the costing of the shell & tube HE.
Table of Contents
Sections of Equipment Costing Sheet
So, first let us discuss the various sections of the shell and tube heat exchanger costing. Generally, we can divide this in following sections:
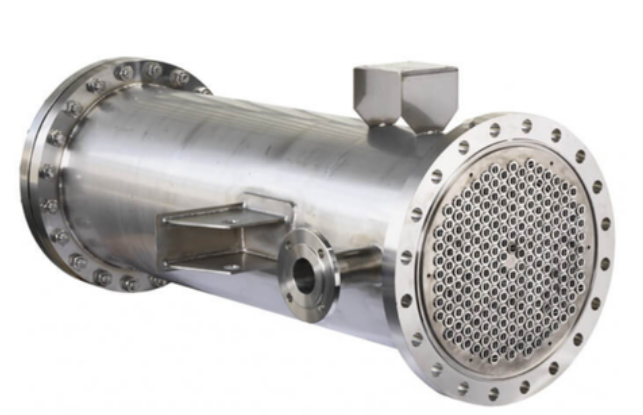
Material Cost
This part includes the cost of material which you procure for the fabrication of the heat exchanger. For costing purpose, we need to consider raw material cost which includes finished equipment weight and waste material both. Waste material is the remaining metal after cutting out the required portion of metal from sheets and pipes. This is around 10% of the finished equipment weight. The various types of material include plates for shell, channel & dish ends, plates for flanges, plates for tube sheets, plates for baffles, tubes, tie roads, nozzle pipes & flanges, material for support, etc.
Fabrication Cost
For the heat exchanger fabrication there are lots of activities involved which are performed by skilled fitters & welders. Based of the fabrication drawing workers do cutting and welding of the plates, tubes, pipes & flanges. Drilling of the tube-sheets, baffle plates and fabrication of the body flanges is done. So, charges of fitters & welders, consumables for welding & cutting (i.e., welding rods, cutting wheels, gas cylinders, etc.), various machine charges, electricity charges, etc., are the part of equipment fabrication cost. This fabrication cost is generally in the range of 30% to 60% of the total material cost. For small size and complicated equipment fabrication cost is considered higher side (i.e., 40-60% of the material cost). While for simple and large size equipment we should take fabrication cost lower side (i.e., 30 to 40% of the material cost).
Other Costs
This comprises various charges like testing and inspection expanses, painting and insulation (if done at vendor site), taxes & freight charges are also the part of this cost. Other than this packing & forwarding is also the charges which add to the final equipment cost.
Format of Shell and Tube Exchanger Costing
Below is a typical format to do the costing for a shell & tube HE, in which you need to provide various data of the shell & tube heat exchanger. To furnish these data, you need heat exchanger data sheet or fabrication drawing.
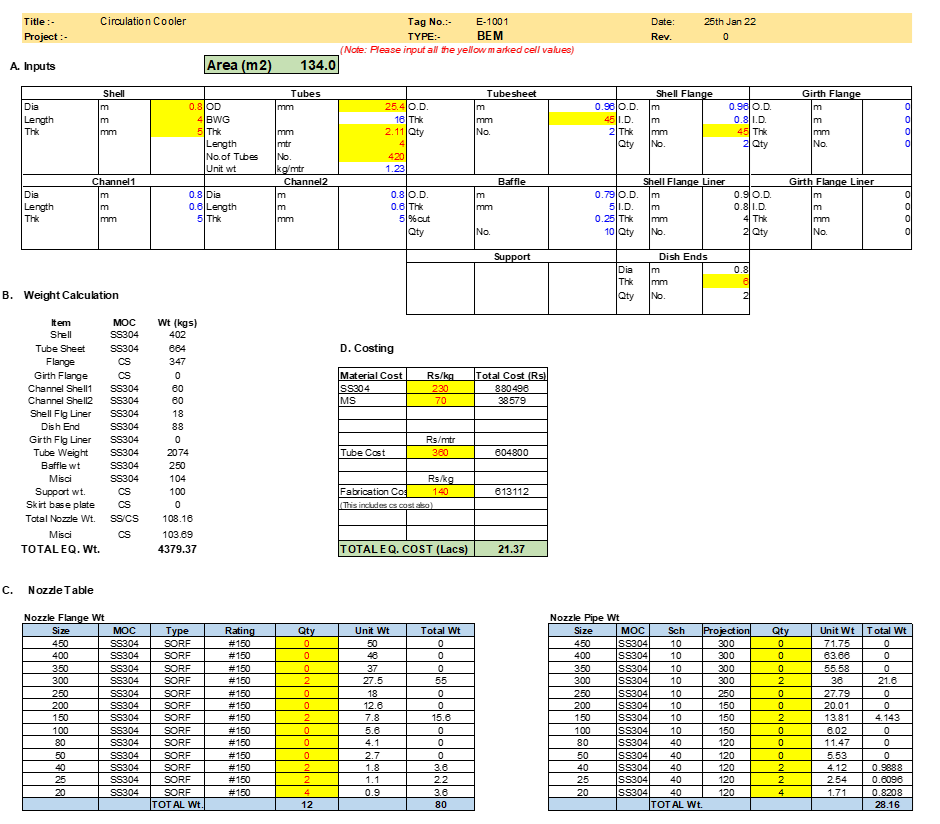
Input Values
Please provide all the inputs as marked yellow, such as diameter, shell length, shell plate thickness, channel shell length, thickness of channel shell & dish ends, number of tubes, tube sheet thickness, flange thickness, numbers of baffles & thickness. Apart from this you can provide the nozzle details in nozzle table for their weight estimation. You can customize this based on your requirement if there is change in flange rating.
Moreover, in case we wish to have lined body flanges we can change this accordingly. For that we need to change the MOC of body flanges from SS to MS and change the total weight for SS & MS accordingly in the excel sheet. Similarly, if there is a change in the type of exchanger you need to modify this excel sheet accordingly. However, this sheet you can use for BEM or AEN type shell & tube heat exchangers costing. Also, here I have considered a BEM type heat exchanger with CS body flanges having SS304 liners to reduce the equipment costing.
Apart from these you need to provide material cost and fabrication cost, which should be latest one. This you can easily get from the purchase department people. To download the excel sheet for costing of shell & tube heat exchanger please click here
.
Conclusion
I am sure this will help you to estimating the cost of a shell & tube heat exchanger. Furthermore, you can modify this calculation sheet as per your requirement to estimate the costing for reboiler, preheaters, vaporizers, etc.
Thanks for reading.