In our Chemical Process Industries, we use centrifugal pumps most commonly. And, for the selection of a proper centrifugal pump we need to provide its technical specification correctly and completely. So, we can see the various important parameters which require in pump process data sheet are available NPSH, flow rate, head, fluid properties, temperature, etc. Moreover, we provide minimum, maximum and normal condition of all above parameters to show the variability in process. It is found that as a process engineer except NPSHA, we provide all the information properly in pump process data sheet. While, providing NPSHA or net positive suction head available data is not estimated seriously and even many times it is not furnished at all. But there are many process conditions when we face cavitation problem in centrifugal pump operation due to NPSH available.
So, in this article we will discuss about NPSH and its possible impact on the pump operation. Moreover, we will see how can we resolve these issues in our plants.
Table of Contents
What is NPSH (Net Positive Suction Head)?
In simple words, NPSH is minimum pressure requirement at the pump suction to avoid evaporation of the liquid. This way we can avoid the possibility of the cavitation inside the pump. The reason behind this phenomenon is the vapour pressure of that liquid at pump operating temperature.
To understand this, let us refer below figure of a centrifugal pump schematic. So, the pressure at inlet (P1) should be sufficiently higher, to keep pressure at impeller eye (P2) greater than liquid vapour pressure. Or we can say to avoid cavitation pressure drop (P1 – P2) > P*, where P* is the liquid vapour pressure at pump operating temperature.
Therefore, sufficient NPSH (i.e., here P1) ensures pump working without liquid vaporizing inside the pump. Inside pump kinetic energy of a rotating impeller converts into the pressure energy and liquid leaves at pressure (P3) from the pump discharge nozzle.
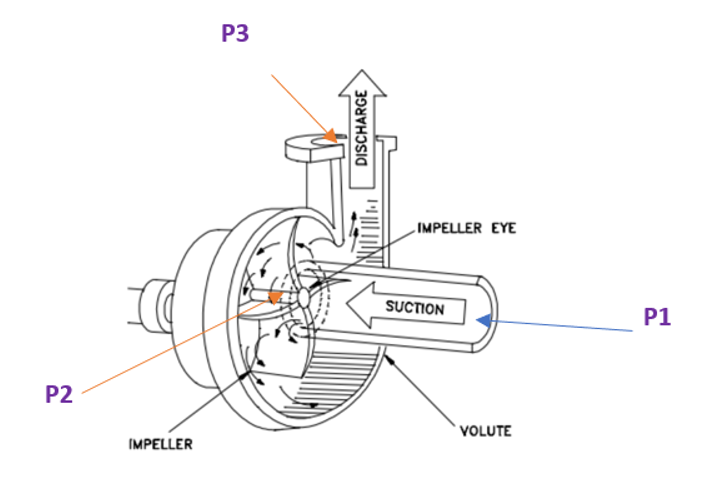
In pump specification NPSHR or NPSH required is the height of fluid required at the pump inlet. The pump manufacturer provides this data and depends on the pump model. Generally, the datum line for this required height is center line of the pump inlet.
So, for a given centrifugal pump, to avoid cavitation during pump operation this NPSHR is always smaller than NPSHA.
How to Calculate NPSH Available?
As we discussed above about NPSHA and NPSHR, in this estimation of NPSHR is the job of pump manufacturer. While, as a process engineer, we are concerned to determine the NPSHA for our pump.
So, to estimate the NPSHA we do a pressure balance from liquid level in vessel, pressure drop in fittings and piping up to pump suction. To understand this please refer the below figure, which is a typical schematic for the installation of a centrifugal pump system.

The available NPSH for above system we can calculate as below:
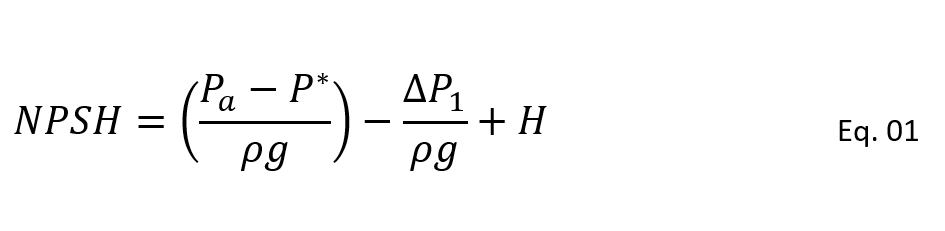
Here, Pa = Absolute pressure inside vessel (Pa), P* = Vapour pressure of liquid at fluid temperature (Pa), ∆P1 = Pressure drop in piping from vessel bottom to pump suction (Pa), H = Static head of liquid in (m), g = Gravitational acceleration (m2/s), ρ = Fluid density (kg/m3)
Example:
A centrifugal pump having 10 m3/h capacity and 30m discharge head is installed above 4 ft (1.2192 m) above the liquid level. Pressure inside the tank is atmospheric and required NPSH is 3.5 m as per the pump supplier. Other information is as below, please evaluate whether this pump will work or not in terms of NPSH requirement.
Pa = 101325 Pa, P* = 26200 Pa, ∆P1 = 3450 Pa, H = (-) 1.2192 m (Because pump suction is above the liquid level), ρ = 865 kg/m3, g = 9.81 m2/s.
Substituting all the data in above equation we get,
NPSH = [(101325 – 26200)/(865*9.81)] – [(3450/(865*9.81)] + [(-1.2192)]
NPSH = 8.853 – 0.467 – 1.2192 = 7.17 m
Since NPSHA = 7.17 m which is greater than NPSHR = 3.5 m, therefore this pump will work without any cavitation problem.
Cavitation Problems & Solution
In our plants we face frequent problem of pumping in terms of flow rate and discharge head fluctuation. The reason of this problem can be because of two possible reasons. First, inlet piping is choked and pump is not getting sufficient liquid at suction. While, another reason can be due to cavitation problem in the pump.
So, remedy in first case is regular checking the strainer and cleaning of same so that pump can get sufficient liquid at suction. Moreover, we can provide a settling vessel in suction line, if there are too much suspended solids present in liquid. This will reduce the strainer chocking frequency and pump will give constant flow at stable discharge pressure.
The cavitation problem, we face more commonly in distillation column bottom pump, specially operating under vacuum. Where liquid inside column bottom is at its saturation temperature. So, small decrease in liquid level or increase in suction line pressure drop can create pump cavitation problem. Apart from this in some installation where reservoir temperature change range is very wide. It can be from ambient temperature to liquid saturation temperature. So, this will also affect the NPSH available in a big way. Also, when we revamp the existing system, there can be too many sharp bends and create large pressure drop in pump suction piping.
Below are some practical solutions which we can apply to resolve the cavitation problem in the operating centrifugal pump.
Provision of Bottom Cooling
We can provide sufficient cooling of liquid in pump suction to avoid cavitation. For this you can refer below figure:
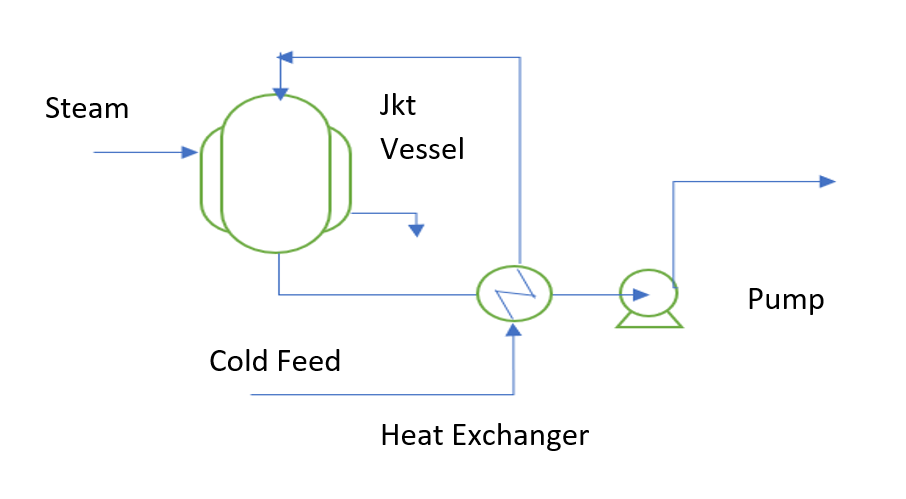
Elevate the Suction Vessel
This way we can provide additional static head to the pump, which will enhance the NPSH available for the pump. If it is not possible to lift the vessel, tank or column, we can install the pump in a pit around one meter deep. Using this technic, we can avoid the cavitation problem in the operating pump.
Reduction of Pressure Drop in Suction Line
Many times, it is observed in suction piping there are lots of bends. Moreover, suction piping size is not proper, always ensure suction piping sizing must be one size larger than the discharge line size. So, we should fabricate suction piping without bends. In case where bends are unavoidable, we should use 450 bends instead of 900 bends. This will reduce the pressure drop in suction piping and enhance NPSH available. This way we can avoid cavitation problem.
Degassing of Liquid
There are many processes where liquid contains gases like ammonia, CO2 or trapped air, etc. During pumping this gas can desorb from liquid, inside the pump and cause cavitation problem. So, we should provide a degasser to remove this free gas from the liquid. To degas the liquid, we can heat it.
Conclusion
Hope this article will help to get insight about NPSH and to acknowledge its importance during pump selection. Also, a process engineer should always evaluate the pump NPSH available. While, in the case of saturated liquid pumping NPSH available estimation is very critical. So, pump required for distillation column bottom transfer specially under vacuum and steam condensate transfer should be checked for NPSH available.
Thanks for reading.