In chemical industries raw materials enter into reactor and reaction takes place to convert them into products. These reactions can be either catalytic or non-catalytic. Reactor temperature and pressure depend on the reaction conditions. In chemical plants some reactions occur at low temperatures, it can be as low as ambient temperature. While some occurs at very high temperatures as high as 500 – 600 0C.
Broadly we can divide Flow Reactors into two categories. First is CSTR or continuous stirred tank reactor and second is PFR or plug flow reactor. In CSTR or Backmix Reactor composition and temperature inside the reactor is uniform and output stream has same composition and temperature as inside the reactor. While in PFR or Tubular Flow Reactor reactants composition and reaction temperature varies across the length of the reactor.
Fundamentally it is advantageous to use CSTR for slow reactions as we can afford high residence time there. Also, regeneration of catalyst is very difficult in fixed bed reactor. Therefore, fluidized bed reactor which is a CSTR, is better choice to carry out the catalyst regeneration process. We can achieve isothermal conditions in CSTR easily and temperature control is also better than PFR.
We can see various types of fixed bed reactor installations in chemical industries. All of them can be divided in two categories based on the heat exchange criteria during the reaction. First category is where we are not removing heat from the reactor and product temperature rises adiabatically during the reaction. In second category we try to maintain the reactor bed temperature by removing heat, using heat transfer fluid. This way we try to achieve the isothermal condition inside the reactor tubes. In below section we will discuss these two types of fixed bed reactors in details.
Table of Contents
Adiabatic Fixed Bed Reactors
We use adiabatic fixed bed reactor where heat of reaction is very small. Or in other words heat of reaction can be managed with feed temperature control only. Simultaneously reactions are less temperature sensitive. In this type of reactors generally, we heat the incoming reaction gases to the ignition temperature of the catalytic reaction. And the adiabatic reaction temperature control is often coupled with heat exchange between the incoming reactant gases and exiting hot reaction gases. This way adiabatic reactor operates in so-called auto thermal reaction control mechanism. This we can understand from below figure.
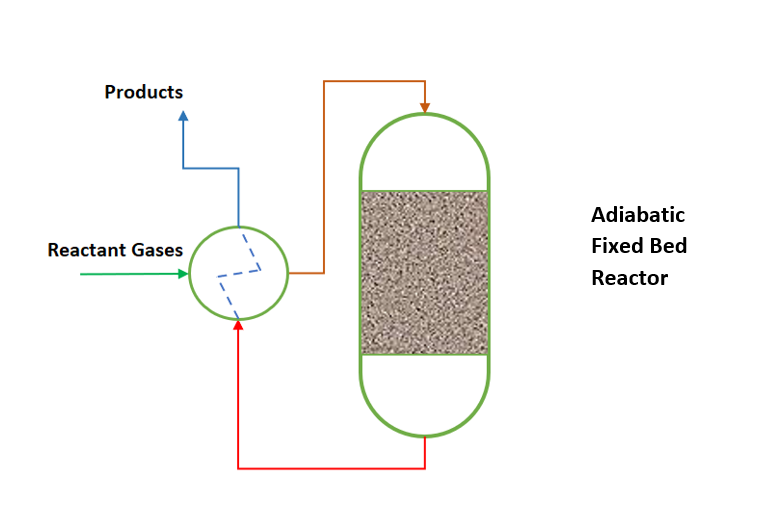
Non-adiabatic Fixed Bed Reactors
While non-adiabatic or isothermal fixed bed reactors we use where, heat of reaction is too high and desired reactor temperature control is not possible by feed temperature. Moreover, reactions are too much temperature sensitive. If reactor temperature is not controlled reaction can lead to run-away conditions. In such cases either we use external cooling or a multitubular fixed bed reactor as shown in below figure.
To maintain isothermal conditions in reactor tubes, we fill catalyst & inert pellets in different ratios. At the top side reactants concentration is highest therefore we maintain lowest concentration of catalyst. While at the bottom side of reactor reactants concentration is lowest therefore, we fill 100% catalyst. For example, we can use filling patterns in 4 equal heights from top to bottom in ratios of catalyst to inert such 25:75, 50:50, 75:25 & 00:100. This way we can achieve isothermal conditions across the catalyst bed height. However, there can be catalyst & inert filling in 2 or 3 equal segments also.
During catalyst filling we need to ensure equal pressure drop across all the tubes. This we do to avoid channelling problem in the tubes. Because if there is a substantial variation in pressure drop across the reactor tubes, then lowest pressure drop tube will receive highest flow. And high pressure drop tubes will receive lower reactants gas flow rates. This will affect the conversion and reactor capacity, moreover this can lead to hot spot problem also.
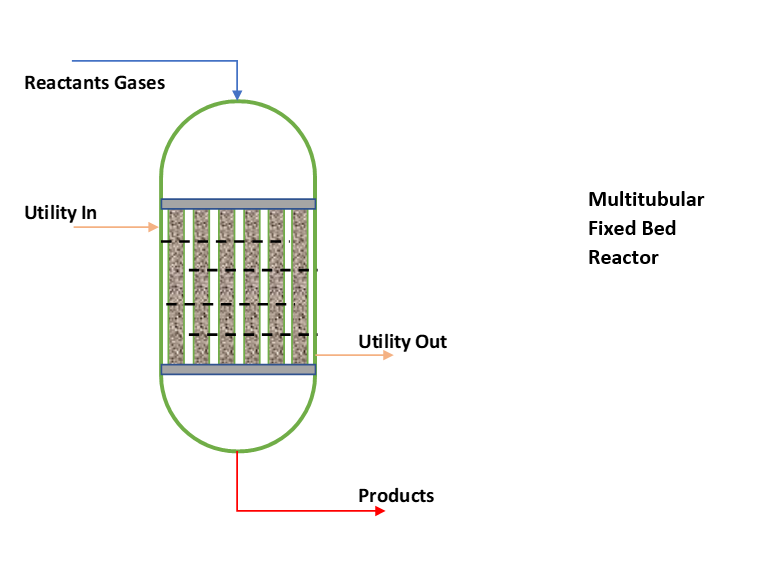
Catalyst for Fixed Bed Reactors
In a fixed bed reactor catalyst is the heart, without which chemical reaction is not possible. We can see these catalysts are used in various shapes and sizes. Commonly we use cylindrical pallets which has L/D ratio 1.0 and size is 1/6 of the reactor tube inside diameter. Therefore if 25.4mm outside diameter tube will have 4mm size catalyst pellets. You should know higher size pellets will increase the channelling problem in tube bed which will reduce conversion and capacity of the reactor. On other side at smaller size pellets will increase the pressure drop across the reactor. Subsequently this will increase your operating cost as we require higher pressure compressor to feed the reactant gases into the reactor.
During reaction in fixed bed reactor we can divide the reaction process in following steps:
- In first step reactants diffuse from the gas space through the outer gas – particle boundary layer, macropores, and micropores of the catalyst pellet
- Chemisorption of the reactants on active centers in the catalyst
- Reactants reacts at catalyst surface
- After reaction desorption of the products
- And finally, products back-diffusion into the gas space
Multitubular Fixed Bed Reactor
A fixed bed reactor is heterogeneous reaction system. In chemical industries, we can find this type of installations for gas phase catalytic reactions most frequently. As we can see in above figure, catalyst is filled inside the tubes and heat transfer media circulates in shell side. Fundamentally, you can see a multitube fixed bed reactor is like a shell & tube type exchanger. Where reactant gases enter tube side through bed of solid catalyst. And reaction takes place to convert the reactants into products. The temperature of reactor is controlled by heat transfer media circulation in shell side.
Selection of heat transfer media depends on the reaction temperature. For highly exothermic reaction up to 350-380 0C, we use thermic fluid. In case of higher reactor temperatures, we use molten salts circulation to remove heat of reaction.
Since solids are poor conductors of the heat, therefore we face problem of hot spots formation inside the tubes. Many times, this hot spot may lead to localized adiabatic temperature rose and can melt the tube wall metal. Which cause shell side thermic fluid leakage into the reactor product outlet.
In fixed reactor, we face problems such as catalyst bed temperature control, channeling of reactants, catalyst replacement. However, fixed bed reactor gives highest conversion per weight of catalyst in comparison with any other type of reactor. Therefore, for given production rate multitube fixed bed reactor size is smaller in comparison with a fluidized bed reactor with is a CSTR.
Design Equation for PFR
Let us assume we are feeding a chemical ‘A’ into the reactor and which is converting into product ‘B’. The molar flow of ‘A’ is FA (kmol/h) and conversion is ‘X’. This is an exothermic reaction having heat of reaction -∆Hr (kcal/kmol). Now we can write a component mole balance for ‘A’.
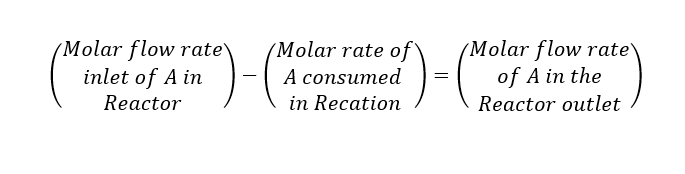
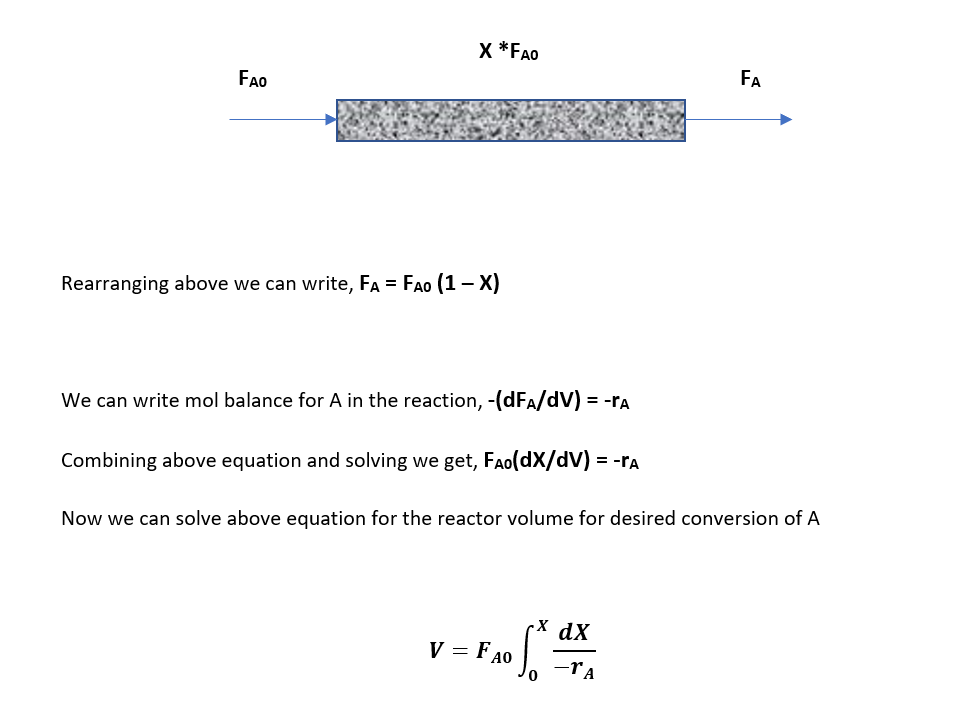
Above is the design equation for a plug-flow reactor to solve this we need to know the rate of reaction -rA. Which will tell us how the rate of reaction varies with the concentration of A, from this we can find relationship between -rA and X to solve the PFR design equation.
Operation & Controls of Fixed Bed Reactor
A typical schematic process flow diagram and controls for fixed bed reactor is something like as given below. This works for both exothermic and endothermic reactions.
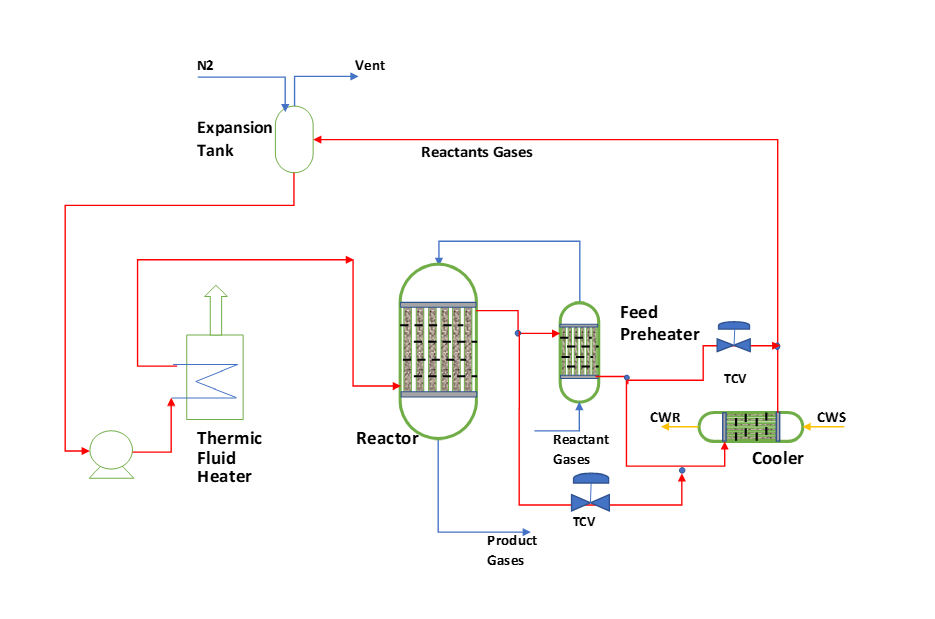
For start up we heat the reactor system to reaction temperature. We supply heat to the system by FO/NG furnace or an electric heater using thermic fluid circulation. After achieving reaction temperature, we start feed into the reactor and reaction starts. We stop the furnace and thermic fluid remain circulating. This circulating thermic fluid takes the heat from reactor and reject the heat in feed preheating. To control Reactor feed temperature (i.e., feed preheater outlet temperature) we provide a TCV in bypass line of feed preheater. During reaction, you should maintain thermic fluid supply temperature around 5 0C from the reactor temperature. This temperature control we do using TCV in the bypass of the cooler.
Where ever reaction heat generation is very high, there we can install waste heat boiler to generate waste steam also.
Another area for waste heat recovery can be the reactor outlet. This heat we can use for feed pre-heating or LP waste steam generation also.
Safety Measures in Fixed Bed Reactor
For highly exothermic temperature sensitive reactions there are chances of reaction runaway. At reaction runaway there will be a sudden release of energy which leads to adiabatic temperature rise and increase in reactor pressure. Therefore, to eliminate the explosion in reactor during runaway condition we provide rupture disc and safety valves. The rupture disc set point is higher than the safety valve set point pressure. Whenever pressure rises inside the reactor, first safety valves pop up to release the pressure. In case if pressure is not reduced by safety valve pop up then rupture discs blown away to release the reactor pressure. We should connect Safety valves vents to the scrubber or quench vessels, this way we can avoid the hazardous gases emissions in vicinity. However, rupture disc vents must be open to atmosphere. Because it can increase the back pressure after rupture disc busting and apply thrust at reactor support and connected piping. Which can damage the reactor support and connecting piping also.
Conclusion
This article was to give an overview about fixed bed reactors in chemical industries. We discussed the operation and controls. Moreover, challenges in fixed bed reactors operation and possible ways to handle them.
Furthermore, we should look into the digital transformation of the fixed bed reactor. Real-time data analysis will help us to optimize the reactor parameters in real time. Which will help us to improve reaction yield and stable reactor operation. Machine learning and artificial intelligence can avoid the runaway conditions by predictive modelling. Moreover, this can help us to understand the catalyst behavior with respect to the various operating parameter like feed rate, concentration, temperature, pressure etc. We can use this analysis to enhance catalyst life.